Keeping Everything in Check
PolyWorks® Cuts the Symmetry and Alignment Check Time on Bombardier's CRJ Series by 75%.
As the airplane touched down on the runway, an unexpected force of impact with the ground resulted in what is commonly referred to in the aviation industry as a "hard landing". Considered a frequent incident, each pilot is expected to experience at least one hard landing over the course of their career. Whether due to meteorological conditions, mechanical problems, an overweight aircraft, pilot error, etc., a hard landing can vary in seriousness from simply causing mild passenger discomfort to resulting in extensive damage to an airplane. So when a hard landing occurs, the airplane must be checked for structural damage before its next flight. At Bombardier Aerospace, this is where the Ground Support Equipment team comes in.
The world’s third largest civil aircraft manufacturer, Bombardier Aerospace designs, manufactures, and supports innovative aviation products for the business, commercial, specialized, and amphibious aircraft markets. Dedicated to setting new standards of customer care and aircraft availability, Bombardier offers a comprehensive range of support and services to its customers. Within its Customer Support Group lies the CRJ Ground Support Equipment team, which consists of experts committed to resolving technical issues—to keep the aircraft flying.
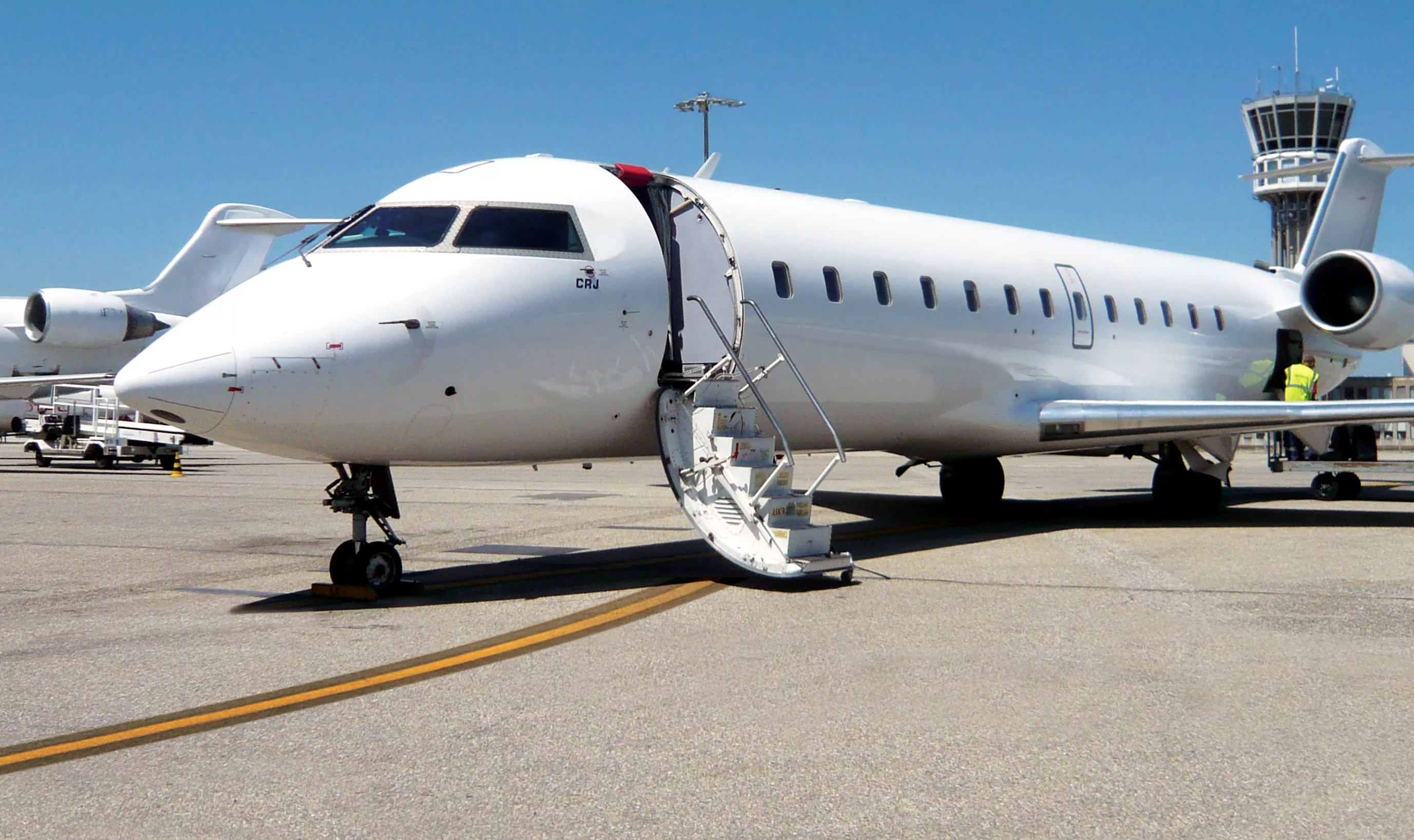
Knowing that a grounded plane can sum up to $100K/day in lost revenue, the CRJ Ground Support Equipment team is dedicated to working around the clock,and across the globe, to return aircraft to service as fast as possible.
The CRJ Ground Support Equipment group focuses on the commercial aircraft division, and lately on Bombardier’s CRJ NextGen Series of regional jets. When an incident occurs with an airplane requiring a symmetry and alignment check to analyze its structural engineering (such as the result of an airplane being hit by a baggage transporter or a jet bridge, or after undergoing a hard landing), a notification is sent to the CRJ Ground Support Equipment group, and the In Service Engineering team is dispatched, on short notice, to any location worldwide. "Knowing that a grounded plane can sum up to $100K/day in lost revenue, the CRJ Ground Support Equipment team is dedicated to working around the clock, and across the globe, to return aircraft to service as fast as possible," said Benoit Roby, CRJ Ground Support Equipment Coordinator at Bombardier.
Once the In Service Engineering team is on location, they will make a diagnostic to determine whether the incident has caused any deviations or damage to the components or to the structure of the airplane that may impact its airworthiness limitation. This diagnostic is done by inspecting the airplane, which includes performing a symmetry and alignment check to expose damage that could otherwise go unnoticed. Then after inspection, if the aircraft is out of specification, maintenance is performed. Once completed, a final symmetry and alignment check is done to ensure that the airplane is once again airworthy.
Symmetry and Alignment Check
A symmetry and alignment check is a dimensional verification of the aircraft's airframe to determine whether its wings and tail are symmetrical to the longitudinal axis. The symmetry check includes inspection of: fuselage vertical deviations, horizontal stabilizer dihedral, engine vertical deviations, engine horizontal alignment angle, fuselage horizontal deviations, wing and horizontal stabilizer alignment, vertical stabilizer alignment, wing incidence and twist check, landing gear check, as well as the symmetry of the winglets. The alignment check of the aircraft’s structure means that the position relationship of each major component must be inspected; this includes inspection of the wing group, tail group, and fuselage group.
Prior to the check, specific conditions must be respected to ensure the precision of the measurements, namely, the aircraft should be inside a closed hangar where air currents or sunlight will not interfere with the alignment readings, the motors should not have operated within the past four hours, all of the fuel tanks should be drained, and the aircraft must be in a neutral/level position (i.e., mounted on jacks with its weight evenly spread out).
The Challenge
The Traditional Method
Traditionally, the symmetry and alignment check has been performed by using the plumb bob and datum plane method. This involves taking manual measures using plumb bobs, precision optical levels, transit rulers, tape, and numerous geometrical accessories that make up the symmetry and alignment kit. However, each kit is aircraft-model specific, meaning that when it’s in use, its accessibility is limited. Also, the traditional method requires two technicians and, in the best-case scenario, takes between 12-14 hours to complete.
To perform the check, target points are taken relying on the symmetry screws located on the airplane as datum points. The plumb bob line is then dropped to the floor and manually measured. Due to the extraordinary size of the airplane, obtaining the measurements is both time consuming and physically demanding on the technicians. Add to the equation the fact that reporting is done manually, two technicians must be present: one to take the measures and one to record the results. The physical size of the symmetry and alignment kit used in the traditional method poses altogether another set of challenges. Since the kit comes in an oversized crate, simply ensuring that the shipment follows the mobile team being dispatched to an international location is a feat.

Taking measures manually requires time and patience to ensure precision.
Additional costs, delays, and customs issues are common occurrences. These complications have, on occasion, resulted in the team being forced to wait for the kit upon their arrival, making their time unaccountable during the wait. Also, shipping the kit back to the initial destination poses another set of problems because the equipment is packed by another crew, meaning there’s the risk of damaging or misplacing tools.
"After selecting the portable 3D hardware, I turned to our specialists in measurement systems of tooling services, and they highly recommended PolyWorks®." Benoit Roby, CRJ Ground Support Equipment Coordinator at Bombardier
Roby and his team reached the point where they needed to simplify their symmetry and alignment process with a portable system common to all airplanes. "Transport of the traditional symmetry and alignment kit had considerable drawbacks, which led us to consider using a 3D scanning solution, yet we were looking for a solution that would not affect the input or the output of our reporting system," said Benoit Roby. The goal of the CRJ Ground Service Equipment team was to eliminate equipment, save time, and make the measurement instruments as simple as possible since not all technicians are metrology specialists.
The Solution
The 3D Metrology Method
Roby’s team opted for the portable Leica Absolute Tracker AT401 and the 1.5" Corner Cube Reflector (CCR) combined with InnovMetric's PolyWorks|Inspector™ software. The selected 3D metrology method provides a universal solution that is compatible with all aircraft—making limited accessibility to the tools a thing of the past. "The new solution is universal, portable, and fits right in our carry-on; this is a huge plus since we don’t even have to check in the equipment for air travel," said Roby. Add to the equipment a laptop and a homemade stand onto which the laser tracker is mounted, and the symmetry and alignment kit is complete—greatly simplifying transport logistics.
Another benefit of the portable 3D metrology solution comes with the fact that the previously mentioned best conditions for performing the symmetry and alignment check cannot always be respected. With the flexibility and robustness that this solution now provides, some of the preparation steps may be altogether eliminated, reducing logistic constraints.
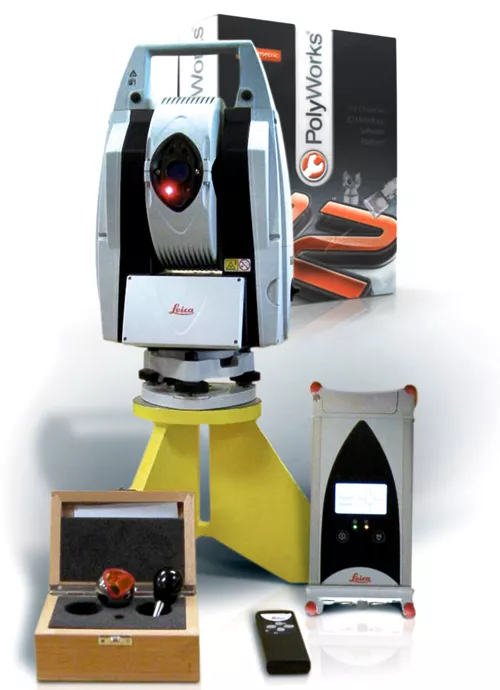
The selected 3D metrology solution fits in carry-on.
What once took two men and 12 hrs to perform can now be completed with one man in 6 hours—which amounts to huge savings!
Yet the most noteworthy benefit is the major time savings: A symmetry and alignment check can now be completed with only one technician in 6 hrs—and Roby even estimates that they will be able to do it in 4 hours. Add the fact that the previous method often encountered delays during transport; the CRJ Ground Support Equipment group was not able to set a flat service rate. With the 3D metrology method, they can now estimate the costs, which is a significant plus because within an organization like Bombardier being able to plan operations costs is key.
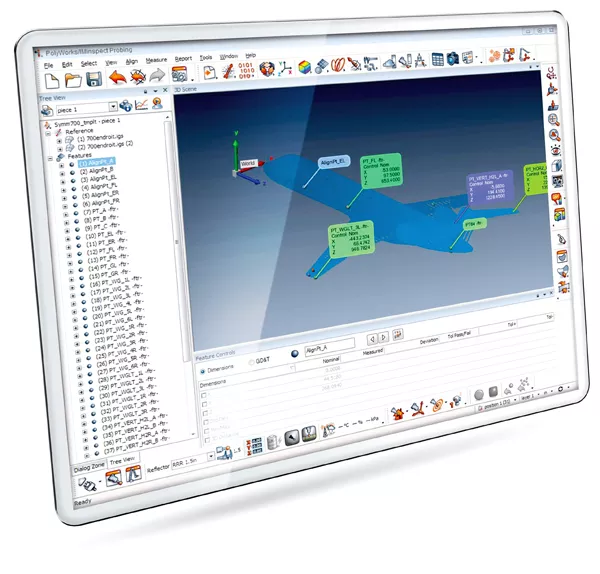
Data of the measures taken with the CCR is immediately available in PolyWorks|Inspector™.
The Benefits
The Application
With PolyWorks, the entire symmetry and alignment procedure is simplified. The technician arrives on location, sets up his equipment and identifies the target points on the airplane. Once this is done, he begins measuring using the CCR, and PolyWorks does the rest. Operations such as determining the axis, moving the device, pairing, and adjusting to match are performed in PolyWorks. As each measure is taken, the data is instantly accessible in PolyWorks, and what’s more, it’s automatically updated throughout the report.
PolyWorks reduces human error, "I have confidence in PolyWorks; if a mistake occurs during the process, it’s immediately pinpointed," said Roby. After measurement of the target points is complete, the technician instantly gets real-time deviations with respect to nominal points from the CATIA CAD model in PolyWorks. Roby finds the interoperability of the software intuitive. In fact, the ease with which PolyWorks handles the model imported from the CAD software, as well as the facility to generate reports were the key factors that influenced Roby’s buying decision.
Reporting
By using PolyWorks, it’s now easier than ever to generate reports. The results are exported to Excel and the standard report format in place remains untouched. "Due to the fact that we must adhere to the strictest international standards, we needed a solution that would not impact our model file. PolyWorks is easy to understand and use, plus it complies with our standards," stated Roby. PolyWorks offers the reporting flexibility that the In Service Engineering team needs in the field since reports can now be done in real-time. Moreover, the PolyWorks technical support group closely collaborated with Roby's team to create reports adapted to their reality. The result: Reports are optimized, yet there's no impact on the report model since the input and the output are exactly the same.
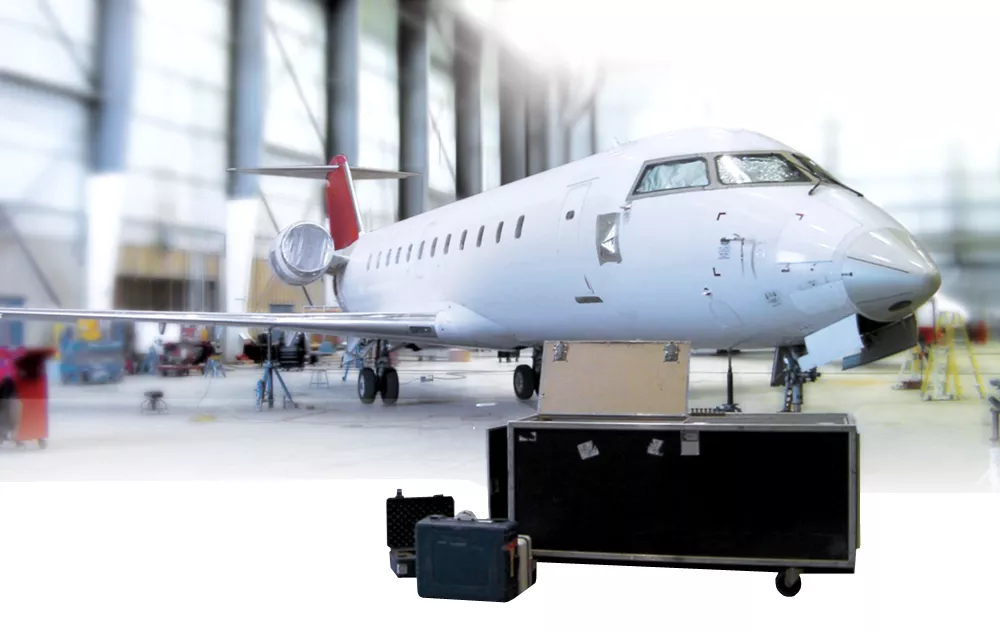
Conclusion
PolyWorks was initially purchased to assist the CRJ Ground Support Equipment team with their symmetry and alignment check, and it has proven that it can go beyond. "PolyWorks offers the versatility that we need. We purchased this product for one purpose, and we’ve started to use it for our mapping needs," stated Roby. By integrating PolyWorks into their inspection process, Bombardier reduced by 75% their symmetry and alignment check time, and with this in mind, PolyWorks is in the process of being evaluated for the symmetry of amphibious aircraft.
Over the course of an aircraft’s lifecycle, it is likely to sustain some form of structural damage, and due to this, damage assessment will remain an essential step in repairing an aircraft. Fortunately, there exist proven solutions that assist inspection crews and help get the aircraft back in the air as fast as possible—reducing downtime, saving money, and contributing to safer air travel.